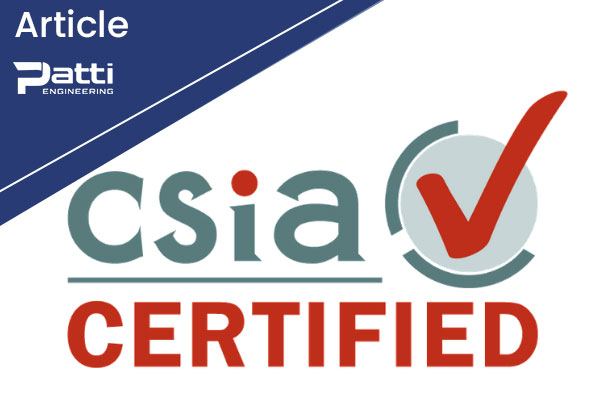
How CSIA Certification Has Made Patti Engineering A Better Company
Being CSIA certified has been perhaps the biggest driver of improvement for our business. CSIA certification is not just a box to check or another shiny gold plaque to hang on the wall. The process is intense and thought-provoking, and the changes that it can drive for a control systems integrator are remarkable.
In order to be certified, we are audited on the guidelines set forth in the Best Practices every three years. Patti Engineering has been certified five consecutive times. What are the Best Practices? The Best Practices are a manual developed over the last 2+ decades from members of the CSIA, many of the leading system integrators. These guidelines focus mainly on the business side of running a control systems integration company (finance, project management, documentation, etc. – not how to use specific technologies). The Best Practices lay out the ‘what’ but each company decides the ‘how’. This means that we can adapt the knowledge to our own needs and applications. It also means that as an organization, we have to think critically about how to improve our company.
Throughout the years, we have made improvements and modifications to our financial systems, our marketing approach and our HR procedures. Recently, our biggest push has been taking our project management to the next level and systematizing our procedures across the company.
One of the major changes we have made is separating the roles of project manager and lead engineer. This shift has allowed each person to wear fewer hats. The project manager worries about lead time, cash flow, budget, hitting milestone dates, and serves as the primary point of contact with our customer. The lead engineer can then focus almost all their time on simply engineering the best solution for our customer. If one person performs both roles, it can be easy to overlook the details on one side or the other.
In making project management one person’s sole priority, we have tightened up our procedures around several areas: writing onsite readiness checklists, hardware lead-time planning, internal and external kick-off meetings, customer communication, and project risk management. It’s not that these are new things – we’ve always done them – but by formalizing more of these processes, we reduce the risk of missing something or making a mistake. “By being intentional with our documentation, the whole project is smoother,” says Nick Hitchcock, PE, our senior project manager, who has been instrumental in making these shifts.
One example of this is our risk assessment procedure in our proposal process. Considering risks has always been a part of our projects. Now, we write out all possible risks and discuss mitigation strategies as a group in our internal kick-off meetings. This holds us accountable to developing an exhaustive list and allows us to access more ‘institutional knowledge’ by discussing it internally. By including this on our project checklist, we ensure we don’t overlook this step. Weekly project check-ins ensure the potential risks and potential solutions are constantly updated. We now also present these initial risks to our customers upfront, ensuring that both sides are prepared to mitigate risk and increasing project success.
This has proven especially important on large projects with multiple phases and/or multiple players. For example, one recent project involved redoing all the machine networks in the entire plant. As you can imagine a small mistake could have a big impact. We started with a robust kickoff meeting with the customer discussing all of the goals and identifying potential risks. Then, our project manager set up a small-scale test on the first install weekend. We had a roll-back plan before we even started. As we all know, there’s almost always an unexpected glitch. By setting up the small test upfront, we allowed ourselves maximum time to address those issues. Things went wrong that first weekend, but we identified all the holes and talked to the customer. In fact, we set weekly meetings with the customer to coordinate each of our sides of the project. These meetings allowed us to be intentional and the added communication meant that we all recovered quickly from anything that went wrong. Each weekend install, we were executing better and better, and the project finished on time.
These changes that we have made are not earth-shattering. But they do greatly reduce the annoying little problems that add up over time. We are immensely grateful for the collaboration of the CSIA that has shared their collective centuries of lessons learned.
Related categories: Blog Company CSIA