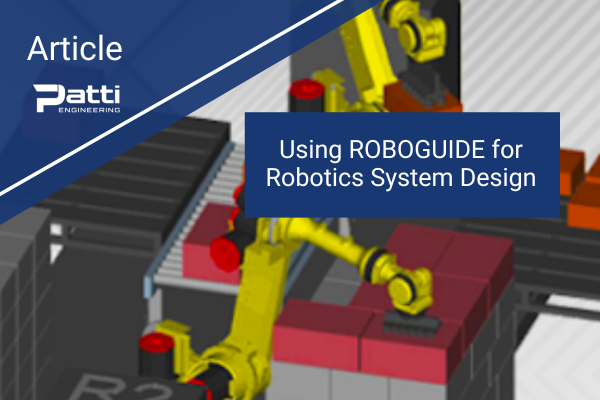
Using ROBOGUIDE for Robotics System Design
ROBOGUIDE, a FANUC 3D simulation software used for the design and simulation of robotic systems, plays a key role in Patti Engineering’s robotic project workflow to deliver optimal robotic solutions to clients. This article highlights some of the ROBOGUIDE features Patti Engineering uses during a project’s design and development phase to select the appropriate robot and configuration to meet our client’s project goals.
ROBOGUIDE is an offline software simulation tool developed by FANUC, a global leader in industrial robotics. ROBOGUIDE allows users to design, simulate, and validate robotic systems within a 3D virtual environment. Every FANUC robot has been modeled for use within the software to accurately simulate and analyze the behaviors and capabilities of different robots, ensuring the robot selected is the best fit for the application and will function as intended. Utilizing this tool during the proposal process allows us to demonstrate to clients a proof of concept to show the proposed new robotic cell will accommodate the equipment and application needs while meeting our client’s desired cycle time requirements.
Beyond showing proof of concept, Patti Engineering’s team uses ROBOGUIDE to support project planning, design, and implementation, including verification of cell layout and robot reach, path programming, offline programming, cycle time analysis, and system lifespan analysis. Ultimately, this allows our engineers to optimize and debug the robotic system offline to minimize downtime or lost production during onsite installation and commissioning.
Figure 1: Robotic cell simulation using FANUC’s ROBOGUIDE software
Verification of Cell Layout and Robot Reach
ROBOGUIDE is used to verify that the selected robot has the required reach to efficiently perform the proposed tasks. Typically, we prefer to use the smallest robot possible for the operation, as smaller robots are faster. This software tool helps us determine the most appropriate robot model and options.
By utilizing ROBOGUIDE’s computer-aided design (CAD) library or importing a CAD model, ROBOGUIDE creates a 3D visualization of the spatial relationships between the robots and their surroundings. A detailed model of the entire work cell layout including fixtures, tables, machines, conveyors, etc. can be built in the virtual 3D environment to accurately simulate and analyze the behaviors and capabilities of different robots and options, ensuring the robotic work cell will function as intended. Potential design issues can be identified and addressed within the virtual environment. Using these visualizations, the layout and functionality of all components can be thoroughly evaluated and tested within the virtual environment.
For the project depicted in Figures 2 and 3, ROBOGUIDE allowed us to verify that the placement and reach of the proposed robots suited the application.
Figure 2: In this work cell, using ROBOGUIDE ensured that the selected robot (FANUC M-710/C) could reach the tray locations (top right) and both stacks of 10 trays in each tote. It also demonstrated the optimal placement of the robot for reachability.
Figure 3 (Close-up of the top left robot from Figure 1): ROBOGUIDE helped determine the best orientation for this robot, enabling it to reach all the trays to its left and right, as well as the two conveyors behind it.
Figure 4: 3D simulation of a robotic work cell
Path Programming
Once all components of the cell are placed within the ROBOGUIDE 3D environment, the robot’s path of motion can be programmed. Path programming is accomplished using the same FANUC teach pendant interface used for programming physical robots. However, robotic paths can also be programmed using CAD models and part geometry as points of reference, streamlining the design process and reducing the need for more tedious manual programming. For example, when tasked with dispensing a bead of sealant, the path can be created using the nozzle of the dispensing tool as a reference point. The spatial coordinates of the object receiving the sealant – in this case the CAD model of a transmission case – is used to define the exact location where the sealant needs to be applied. This approach is much faster than manually teaching each point, and the program is directly transferable to the physical robot.
Joint moves are preferred over Cartesian-based moves, a topic covered in a previous blog. Joint moves are generally preferred for their speed, overall system performance, and minimized cycle time. Deciding between fine and gross moves is important, as fine moves are used for tasks requiring high accuracy, such as deburring, where the robot must maintain a millimeter-level tolerance to effectively track and remove burrs. Gross moves, in turn, facilitate quick transitions between different areas of a work cell where precision is less critical, ensuring the robot performs tasks efficiently while maintaining accuracy where it matters most.
ROBOGUIDE also proves useful when designing lines with multiple robot operations. ROBOGUIDE simulation can be used for a line that has 20-plus robots. It can simulate all the robots working together with fixtures opening and closing, conveyors moving, and cars on skillet conveyors. Patti Engineering recently simulated a two-robot operation, one tasked with picking up objects off a conveyor and the other loading trays, once full, into tote bins. The simulation enabled engineers to account for the robots sharing the space and avoiding collisions.
Offline Programming
Once an engineer has successfully simulated the necessary programs in ROBOGUIDE’s virtual environment, these programs can be loaded directly into the physical robot, saving system programming time.
The transition from a simulated environment to real-world application depends largely on the nature of the task. With applications such as a typical palletizing job, suction cups pick up boxes and exact precision is not required. In these cases, very little touchup of programming points in the field is needed. Similarly, tasks such as painting or spraying lubricants do not require a high level of location accuracy, making offline programming highly effective. Alternately, tasks involving precise assembly of parts with minimal clearance often require manual programming to “touch up” final robot locations. Part variance presents some challenges, requiring more program adjustments to ensure accuracy. Precision becomes more important when working with parts that vary. For example, when dealing with deburring, it is crucial to consider precision because every part is a little bit different.
Cycle Time Analysis
Using ROBOGUIDE, a client’s cycle time requirements can be accurately verified. Once a cell’s layout is complete and the robot’s operation is fully defined, the software provides an accurate estimation of the robot’s cycle time. We often use ROBOGUIDE in the initial design of a cell to get a sense of the expected cycle time. For example, we recently used the software for a global medical technology company’s robotic cell. During the project’s proposal stage, we used ROBOGUIDE to show the client the time it would take for the robot to load dunnage trays with eight test kits at a time. The tool helped us prove that we could meet the fast cycle time they required.
System Lifespan Analysis
ROBOGUIDE can provide insight into the potential longevity of the robots by identifying joints that may be overworked. The software calculates the forces, torques, and overall load on each robot joint considering design parameters such as the programmed path and tool mass. Additionally, ROBOGUIDE calculates the duty cycle and average current use per joint, generating a report with this information, allowing the engineer to assess the robotic system design for overall wear and tear.
Robotic Cell OEE Improvements
Beyond ROBOGUIDE’s use for new robotic cell solutions, we can use the software to help improve OEE on existing robotic cells. Whether the existing robotic system is experiencing downtime or there is a need to explore new ways to optimize production processes, the software can be used for remote virtual simulation and validation without any interruption to production. When a client provides access to a backup of their current robot program, we can typically identify opportunities to fix faults and suggest program changes that enhance OEE and overall performance, such as reducing rejects and improving cycle time.
Read about and watch a simulation video showing how we applied this software for a client. Using FANUC’s ROBOGUIDE software, we tested and validated OEE improvements to a robot cell without interruption to production. This project included adding a camera for vision inspection, determining quality pass/fail at the PLC level, and adding a reject bin.
Patti Engineering has extensive experience and expertise in the design and integration of robotic cells. Contact us to learn more.
Related categories: FANUC Robotics